Troubleshooting Common Soapmaking Problems
Soaping can be a wonderfully creative process, but even experienced soapmakers encounter problems. Don't be discouraged! Most soapmaking issues are easily diagnosed and corrected. This guide covers some of the most common problems you might face, along with solutions to get you back on track.
1. Cracked Soap – What's Going On?
Cracked soap is a frequent issue, especially for beginners. Cracks often appear as the soap cools and hardens. There are several potential causes:
- Too Rapid Cooling: Sudden temperature changes can stress the soap. Cover your soap molds with a towel or blanket to slow down cooling.
- Low Bicarbonate Content: Bicarbonate acts as a buffer. If your recipe is low in bicarbonate (usually due to low-lye usage or addition of acidic ingredients like clays), it can contribute to cracking. Ensure your lye calculation is accurate.
- High Lye Concentration (Less Common): While less frequent, excess lye can also cause cracking. Always double-check your lye calculations.
- Temperature Differences: Significant temperature differences between your lye water and oils can also cause issues. Try to keep both within a reasonable range (around 100-120°F is a good starting point, but adjust based on your oils).
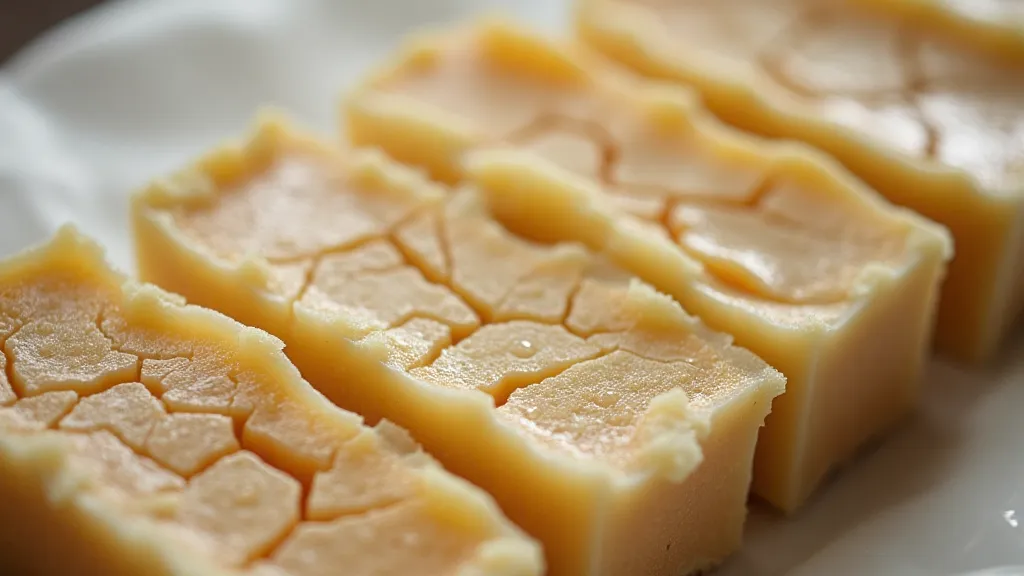
2. Sweaty Soap – A Question of Saponification
“Sweaty” soap refers to a white, powdery film that appears on the surface. This isn’t mold; it's simply unsaponified fatty acids that have migrated to the surface and are reacting with the air.
- Insufficient Saponification: This is the most common cause. It means that not enough lye reacted with your oils. This can be due to inaccurate lye calculations, using too much oil, or using oils with a particularly low saponification value.
- Low Temperature: Cold processes generally have a lower rate of saponification.
- Incorrect Lye Concentration: While usually related to insufficient saponification, a very low lye concentration can exacerbate the problem.
To fix sweaty soap: While the soap is technically safe to use (the fatty acids are present in small amounts), the sweat is aesthetically unappealing. Curing the soap for a longer period (6-8 weeks instead of the usual 4) often helps reduce sweating. You can also try a “gel phase” to speed saponification.
3. Ashing – Dealing with Alkali Reserves
Ashing refers to a darker, dusty appearance on the surface of your soap, often grey or black. It’s caused by an alkali reserve, meaning there's slightly more lye than needed to fully saponify the oils. While not inherently dangerous, an excessive alkali reserve can cause irritation.
Causes of ashing include:
- Slightly High Lye Concentration: This is the primary reason. It's often a result of a small error in lye calculations.
- Use of Certain Oils: Some oils (like castor oil) tend to increase the alkali reserve.
- Adding Acidic Ingredients: While some additives *reduce* the alkali reserve, others (like certain clays) can increase it.
Solutions: Allow the soap to cure for a significantly longer time (up to 12 weeks). This allows the excess lye to react over time. Be cautious when using this soap, especially on sensitive skin.
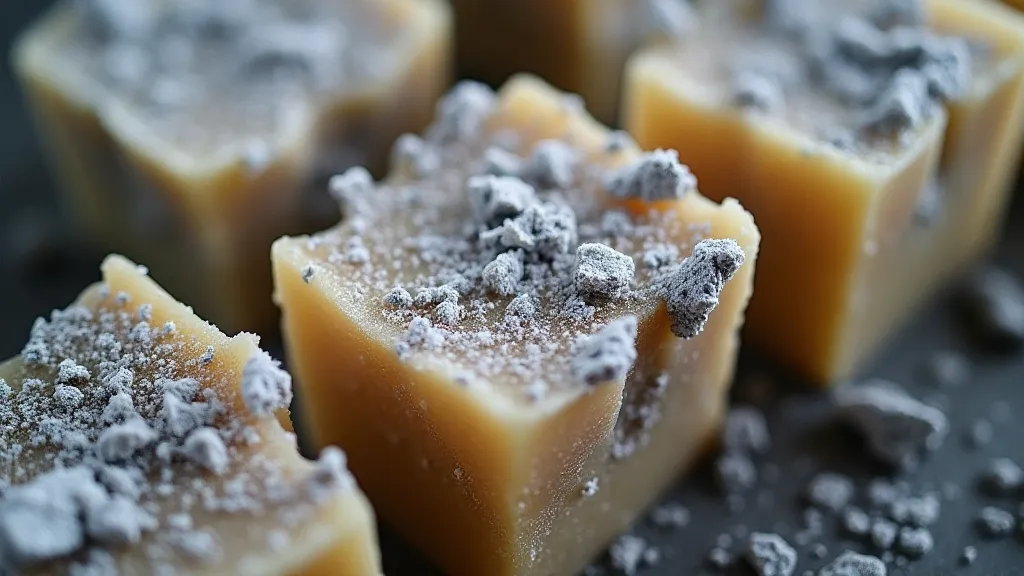
4. Soap That Won’t Harden
Sometimes, your soap remains soft and doesn’t harden properly. This can be due to:
- Too Much Glycerin: Glycerin is a natural byproduct of the saponification process. While beneficial for the skin, excessive glycerin can lead to soft soap.
- Insufficient Saponification: Similar to sweaty soap, insufficient saponification can contribute to a soft bar.
- Use of Soft Oils: A recipe heavy in soft oils like olive oil will naturally produce softer soap.
To address this: Consider adding a small amount of stearic acid (about 1-2% of your oil weight) to add hardness. Ensure accurate lye calculations and use a combination of oils for a more balanced bar.
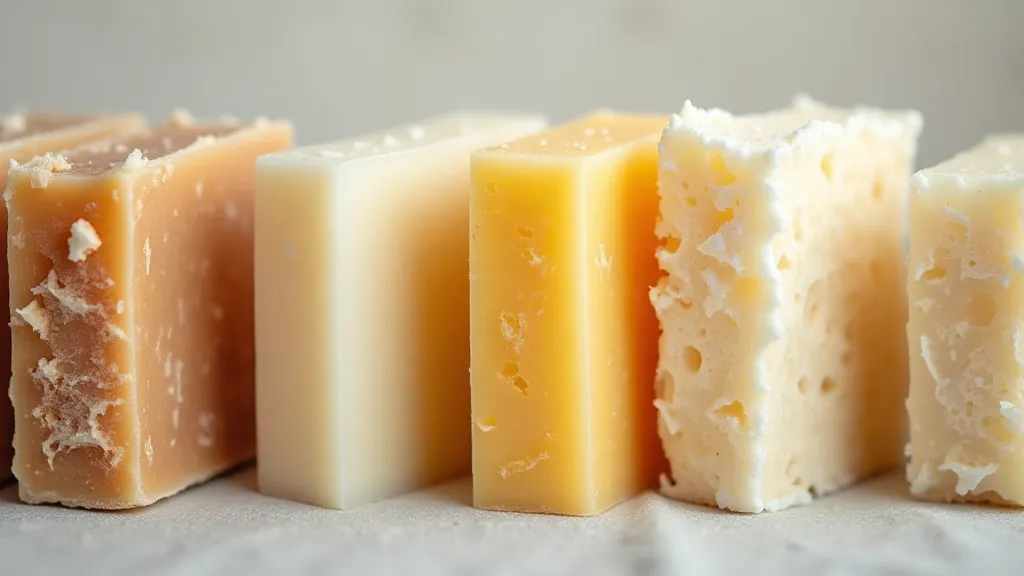
5. Dull Appearance/Lack of Color
If your soap lacks vibrancy or appears dull, here are some potential causes:
- Insufficient Superfat: Superfat is the extra amount of oil in your recipe. Insufficient superfat can impact the visual vibrancy.
- Incorrect pH: Improper lye concentration or inaccurate calculations can affect the pH.
- Colorant Issues: Pigments may not be properly dispersed or may be reacting with other ingredients.
Experiment with a slightly higher superfat percentage. Ensure your colorants are fully dispersed and compatible with your oils.
Remember, troubleshooting soapmaking is all about experimentation and careful observation. Keep good records of your recipes and processes, and don's be afraid to adjust your techniques to achieve the perfect soap!